Key takeaways:
- 3D printing increases creative freedom while cutting the cost of making complex products.
- 3D printing is reinventing manufacturing by moving production closer to the end-consumer, opening possibilities for new business models.
- Wipro’s 3DAssess uses proprietary algorithms to automatically check 3D models for potential geometry, topology, and wall-thickness related issues to validate the overall integrity of the models to be 3D printed.
- Wipro’s 3DAssess automatically performs manufacturing feasibility assessment through integrity checks, types of material used, type of 3D printers used, manufacturing techniques, and the optimum number of parts.
- Wipro’s engineering and process consulting service helps integrate 3DAssess with leading PLM solutions for transmitting inputs to 3DAssess and for carrying out detailed redesign of 3D printed parts for robust performance.
Innovation With 3D Printing
These days, we hear a lot about 3D printing (or additive manufacturing (AM)), although it is unlikely to replace existing production methods in conventional manufacturing in the near future. Adoption of AM in mass manufacturing is likely to remain small due to the high cost of materials and processes involved. However, the promise of AM is that it opens the door to entirely new manufacturing capabilities and hence to previously unexplored designs and business models.
AM can help increase creative freedom and consolidation of parts while cutting the cost of making complex products thereby making low-volume manufacturing more efficient. Today, AM is best suited for small-batch niche aerospace, medical, and automotive applications. However, AM could help reinvent manufacturing, by moving production closer to the end-consumer as well as by motivating 3D printing machines owners to creatively resolve their current excess capacity issues.
In combination with other technologies such as big data, artificial intelligence, and blockchain, AM could further change the way products are designed and produced, making it much easier for companies to enter new markets on the design and the manufacturing fronts, on an even footing with existing, capital-intensive incumbents. One can expect much simplification of supply chains, as parts and products are printed in-house instead of assembling components from multiple suppliers.
3D Printing for Low-Volume Manufacturing
Examples from low-volume, specialty parts manufacturing are very encouraging today and innovators can be expected to push conventional design and manufacturing boundaries in the near future.1 The ability to rapidly solve problems associated with work holding fixtures and jigs is making 3D printing a favorite among manufacturers. Jabil, a manufacturing services company, claims that all their factories have some 3D printing capability for fixtures, jigs, and tooling, and that in their Auburn Hills plant in Michigan, they have saved 35% on tooling costs and 80% on delivery time by 3D printing tools and fixtures. Honeywell Federal Manufacturing & Technologies claims to have printed more than 60,000 tooling fixtures for product testing and saved $125 million through cost-avoidance in manufacturing of non-nuclear components for national defense systems. 2
The ability to make repairs for aircraft using 3D printing without grounding them for lengthy periods of time is another important area of application. For example, the part may take two to three weeks to fabricate traditionally but it could be produced within two- or three-days using 3D printing. Given that the cost of storing parts is 25% of the cost of making them and that spare parts often must be stored for the life of the product, 3D printing makes good economic sense.3 With improvements in 3D printing technologies, industrial equipment manufacturers who usually have a few thousand spare parts in their databases can make them individually, instead of making a batch of them resulting in locked-in inventory cost.
It is expected that once 3D printing proves itself, the industry for dental aligners will make a near 100% switch to 3D printing in a very short amount of time. Also, the hearing aid industry is seeing nearly a 100% transformation to 3D printing. In general, it is expected that at least 10% of all medical devices will be 3D printed in the near future.4
Despite this growing interest in AM, 3D printing a precision part is not straightforward. Careful preparation of the 3D model of the part to be printed needs to be carried out before sending it to a 3D printer.
Preparing 3D Models for 3D Printing
To ensure that 3D printing proceeds smoothly the 3D model of the part must be checked for the following before sending it to the printer:
- Seamlessness—Unless parts are going to be glued together after the printing process, the model to be printed needs to be made of a single seamless mesh without any openings or “leaks.”
- Hollowness—The cost of 3D printing is based on volume. Hence, it is necessary that some models be printed as a hollow object instead of a solid one. Essentially, from the solid model, the faces are extruded along the surface normal to create a hollow model.
- No Non-Manifold Geometry—If during surface extrusion, edges with more than two faces are created, it results in a non-manifold geometry that the 3D printer cannot interpret. Such a situation needs to be identified and remedied.
- Outward Surface Normals—The surface normals of each face presented to the 3D printer must face outward for the 3D printer to interpret the surface correctly with reference to other surfaces.
- Wall Thickness—When turning a 3D model into a real 3D print, the wall thickness of the surfaces must be given unless the printed part is expected to be a solid.
- Self-Intersecting Surfaces—Intersecting surfaces within the model can make it unprintable and such intersections must be eliminated.
The most common file format is STL (Standard Triangle/Tessellation Language), and most 3D modeling software have the option of exporting the model in an STL file format.
Apart from speeding up early design iterations through 3D printed prototypes, the most common use case for 3D printing is the replacement of conventionally made parts with the 3D printed ones. It saves time for repair and inventory costs. The main question in such a direct replacement is, will the 3D printed part do the job. One can determine, based on the known properties of 3D printed materials, if the replacement part will work or not. However, this may not always be an easy question to answer and will call for some detailed engineering investigation, redesign, and testing. Additionally, the 3D printed replacement part must function when printed several years from when the first replacement part was printed. The question of being able to make a reliable replacement part after several years also needs proper investigation and engineering.
Wipro’s 3DAssess for Accelerating 3D Printing
Manual decision-making about whether a part can be 3D printed is tedious, slow, and error-prone and that can negatively impact the adoption of 3D printing. Wipro’s 3DAssess is a tool for automatically assessing the printability of a part based on the assessment of its 3D model, as well as assessing the manufacturability of the part based on the 3D printing machine planned for use. Additionally, Wipro’s engineering consulting services is offered for redesign of the 3D printed part based on the needs of manufacturability and/or of the part’s performance.
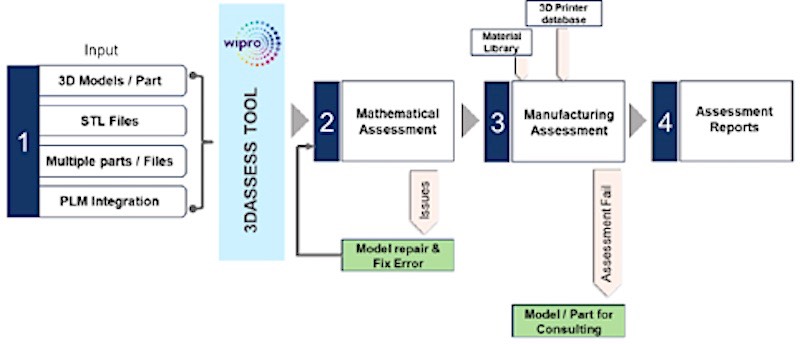
Figure 1—Wipro’s 3DAssess and Consulting for Accelerating the Adoption of 3D Printing (Courtesy of Wipro)
The procedural steps used in connection with 3DAssess are shown in Figure 1. The 3D model of a part or of multiple parts are received by 3DAssess then: First, a mathematical assessment of the STL file is carried out automatically to determine its suitability for 3D printing, based on Wipro’s mesh integrity analysis algorithms. After the STL file-related issues are resolved, the manufacturability assessment for 3D printing is carried out using Wipro’s manufacturing analysis that focuses on the variables pertaining to design and the supply chain. A combined 3D model assessment and manufacturing assessment report is produced while flagging the need for Wipro’s engineering and process consulting if there are doubts about making the parts or about the ability of the 3D printed parts to perform satisfactorily. A few hundred parts can be assessed for their 3D printability in a single step. The capabilities covered by the 3DAssess tool and the associated consulting are briefly described below:
- Mesh Integrity Analysis—Wipro’s algorithms incorporated in 3DAssess help carry out different critical checks including wall-thickness, water tightness, flipped normal, and surface self-intersections for the overall integrity assessment of the 3D model that needs to be printed. The checks applied are listed as: duplicate edge, duplicate facet, enclosed hollow object, check, multiple disconnected objects, non-manifold edge/vertex, inconsistent orientation, and holes. The algorithms help identify issues associated with STL files by color-coding them automatically for ease and speed in correcting them.
- Manufacturing Analysis—Wipro enables detailed analyses for manufacturing feasibility, which includes integrity checks, type of material, type of 3D printer, existing manufacturing techniques, and the required optimum number of parts. Wipro relies on its growing database of 3D printers, OEMs, and materials to make precise recommendations. Wipro’s algorithms also help identify overuse of some materials (e.g., reinforcing fibers, to help save material costs and remove wastage) automatically. Additionally, insights are provided through a comparison of the results of traditional manufacturing with that of 3D printing.
- Assessment Report—Wipro’s 3DAssess provides a report for every component detailing the material and the machine used along with the quantity of material and time required to complete 3D printing. The manufacturing assessment in the report covers the dimensional check, the minimum order quantity, the lead time, and scrap volume. The detailed report helps reduce the turnaround time for assessing optimization potential by increasing the speed of iterations, which would be quite low if attempted manually.
- Consulting—Wipro’s engineering and process consultants are engaged at several levels for enabling 3D printing broadly in organizations of different sizes. At the first level it may involve integration with PLM solutions for product information and ERP systems for supply chain information. In a more detailed scenario, Wipro’s consultants help in detailed redesign of parts intended for 3D printing by making sure that the parts perform in a robust manner. Finally, Wipro consultants have the expertise to help plan the transition to 3D printing-based manufacturing at a larger scale.
Wipro’s 3DAssess has been leveraged in several industrial applications like:
- Parts consolidation in an engine manifold from 15 to 1 while cutting manufacturing lead time by half and improving reliability.
- Molding tool improvement with redesigned cooling channels and using 3D printing, reducing cost of tooling by 30% and manufacturing lead time by 50%.
- Redesign heat sink with integrated fins to improve dissipation by 17% and used 3D printing to reduce manufacturing lead time by 9 days.
- Reduce vehicle accelerator pedal weight by 37% and cost by 7% through topology optimization and 3D printing.
These typical applications of Wipro’s 3DAssess show its usefulness in accelerating the acceptance of 3D printing as a viable alternative to conventional manufacturing and after-sales service when parts consolidation, weight reduction, complex geometries, and small volume parts become clearly relevant for improving competitiveness and profitability. 3DAssess helps enterprise-wide decision-making based on analytics about the feasibility of 3D printing in different stages of the product lifecycle.
Summary
CIMdata has been closely monitoring the progress of AM in the industry, as well as looking into the challenges posed by it with regard to PLM. At this point in time, the chances of AM impacting the traditional manufacturing market seriously doesn’t appear to be very high. However, AM does open the door to distributed and flexible manufacturing of low volume specialty parts where businesses with excess capacity can play a significant role, giving rise to innovative business models. The main thrust of AM today appears to be in work holding jigs and fixtures, mass customized medical devices, and low volume parts for aerospace and defense applications. However, the AM market is significant enough and progressively growing due to some very creative effort, behooving CIMdata to monitoring it carefully.
Although, AM provides the ability for making complex parts that traditional subtractive manufacturing could not do at reasonable cost, if at all, the process of making those parts beginning from their 3D models is not straightforward. The complexity lies in assessing the topology and the geometry of the parts to make sure that the 3D model when sent to a 3D printer produces a satisfactory part. 3D printers today demand a certain level of preparation of the 3D models before they can print them. Also, by just taking the 3D model of part made by conventional manufacturing methods and correcting it for 3D printing, does not ensure that the 3D printed part will perform as expected because of the material change. A redesign of the part made using 3D printing is often needed. Also, the redesign must take into account the fact that the next replacement part may not be printed for several years.
Wipro 3DAssess algorithmically readies parts for 3D printing based on the analysis of the topology and geometry available from their 3D models. Wipro 3DAssess also helps determine whether parts can be made of certain materials on a chosen 3D printer in desired volume within desired time. Additionally, Wipro’s engineering and process consulting services help redesign parts hitherto made by conventional manufacturing methods to be manufactured using 3D printing.
Wipro has considerable experience applying 3DAssess and its consulting services to help manufacturers and after-sales service organizations to leverage 3D printing to replace traditionally manufactured parts for better performance, reduced manufacturing lead times, and reduced cost of inventory. Wipro’s 3DAssess solution, and its engineering and process consulting services jointly form a complete set of capabilities that manufacturers and after-sales service organizations will want to explore when experimenting with 3D printing, while considering innovative products and perhaps business models to disrupt markets to their advantage.