Key takeaways:
- Global value chains are growing more complex and expansive with every passing day. The dynamism in value chain participants, and the pace and complexity of their interactions, demands a highly secure and easy to use solution.
- Eurostep, a company known for their expertise in product data exchange standards, has offered ShareAspace, a standards-based on-premise value chain collaboration solution, for over 15 years. It powers global value chains of leading organizations like BAE Systems, Volvo, Siemens Energy, and the French Army.
- A new cloud-native offering, ShareAspace Design to Manufacturing, builds on this knowledge to support important use cases for smaller firms that have the same complex problems as OEMs but lack the resources and expertise to use more traditional PLM-enabling solutions.
Introduction
Global value chains increasingly need to share intellectual property at an ever-faster pace. Traditional product lifecycle management (PLM) enabling solutions are often not the appropriate choice to handle the dynamism, pace, complexity, and security requirements of these value chains. In addition, some data needed in the value chain may come from other sources such as enterprise resource planning (ERP), maintenance, repair, and overhaul (MRO), model-based systems engineering (MBSE), etc. making the use of a classic PLM system even less appropriate. To meet these needs, Eurostep Group (Eurostep), well known for their work in the global data standards community, leveraged that knowledge to create ShareAspace, their solution to enable secure collaboration across enterprises and value chains. Their success with their on-premise version led to the introduction of a cloud service, ShareAspace Design to Manufacturing, the focus of this commentary.
Research for this commentary was partially supported by Eurostep.
The Need for Global Value Chain Collaboration
Things were much simpler at the dawn of the 2nd Industrial Revolution. In the 1920s industrial behemoths like Ford and their River Rouge complex were vertically integrated, with iron ore, coal, sand, rubber, and other raw materials transformed into electricity and finished products rolling off the assembly line. Yes, there were some components, but this extreme example is just that, an example. It provides a stark contrast to the situation today.
Companies in many industrial markets compete globally. They source mechanical, electrical and electronic, software, and engineering skills globally. What was once a short, compact supply chain has become a global value chain as illustrated in Figure 1. Multiple tiers of suppliers provide a range of value-added components. Those at the higher tiers may collaborate directly with their original equipment manufacturers (OEMs) on key subsystems and components. Those at the lower tiers may build to print or even build to stock. But in most cases, all have to share some level of product data. Most have to get intellectual property (IP) from their OEMs to do their work, and some have to share their IP, at some level, with their OEMs.
It is these types of dynamic global collaboration scenarios that PLM was envisioned to support, including key capabilities like configuration management and engineering change. To CIMdata, PLM is not a technology but a collaborative strategic business approach that can use a range of technologies that may create IP, depending on the products being developed, created, and deployed. But at the core there needs to be strong data and process management to underpin the collaboration. Because there are a range of possible technologies for creating IP there will also be a wide range of data types that need to be stored and managed. These include geometric data, often in proprietary formats. The PLM vision describes enabling seamless collaboration among global collaborators. The reality is often something entirely different.
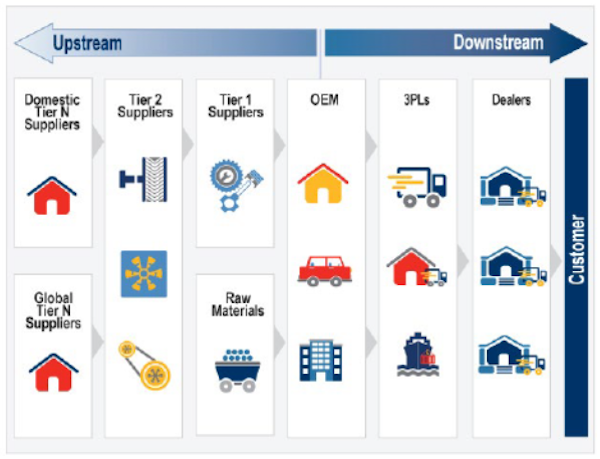
Figure 1—From Vertical Integration to Global Value Chains (Courtesy of EDI Basics (1) )
Data incompatibility issues have plagued digital product development almost from its inception. The proposed answer has many times been standards, but they vary in effectiveness. For product data, early standards like IGES were not strong enough. ISO STEP was going to change all that and did make some improvement but many challenges remained. Success requires a broad commitment to standards and openness, and initiatives like the Codex of PLM Openness and CIMdata’s Aerospace and Defense PLM Action Group have had positive impacts.
But data is only one complexity facing global supply chain collaboration. Even if an OEM has a strong PLM implementation, they may want to limit those partners allowed into their internal systems, particularly those who may be transient collaborators. Some collaborations require sharing of data classified as secret for commercial or defense reasons. To maintain that separation, many companies use systems outside their firewall to enable collaboration. Whether inside or outside the firewall, security is paramount. Yes, all of the data must be protected from outside the collaboration but it also must be protected, selectively, from collaboration participants. Suppliers do not want their OEMs to know too much about their business, lest it be used to demand future price cuts. CIMdata experience with industrial clients shows that today’s collaborator may well be tomorrow’s competitor.
Many companies are looking to the cloud to better support global collaboration. Cloud-based systems are much easier to provision. No servers to buy or admins to run them. For the same reason they are easy to scale up, to add new value chain partners, or to scale down as collaboration needs decrease. With few exceptions, cloud-based systems are potentially available everywhere from a web browser, accessible by PCs and mobile devices. To meet this requirement, Eurostep is introducing ShareAspace Design to Manufacturing, a cloud-native value chain collaboration solution that leverages their experience with their ShareAspace on-premise offering. This new cloud solution was designed to be a no/low touch offering, a vital attribute in their intended markets.
Eurostep’s ShareAspace and the Cloud
Eurostep is well-known for their work on standards that enable product data exchange and collaboration. Founded in 1994, Eurostep has been a key proponent of openness and standards, with a focus on ISO 10303, formally known as “Automation systems and integration — Product data representation and exchange,” but better known as STEP, the Standard for the Exchange of Product model data. STEP Application Protocol 242 (AP 242 or ISO 10303-242) defines “managed model-based 3D engineering,” dictating how 3D content is to shared. (2) In the PLM context, ISO 10303-239, the Product Life Cycle Support (PLCS) standard, is equally important as it defines “what information can be exchanged and represented to support a product through life. (2) In today’s parlance, PLCS helps define the digital thread. Eurostep’s work on standard data formats and structures to support global collaboration was core to their mission. Taking it one step farther, they introduced ShareAspace in 2001, the first value chain collaboration solution built around data exchange standards like ISO 10303, ISO 10303-239, and ISO 10303-214/242.
Eurostep describes this offering as “a technical data repository and publishing platform that enables the sharing of, and collaboration associated with, technical specifications and requirements in order to assure quality by increasing transparency and data management process enablement.” It helps users in a wide range of roles to share data from a myriad of enterprise systems, as illustrated in Figure 2.
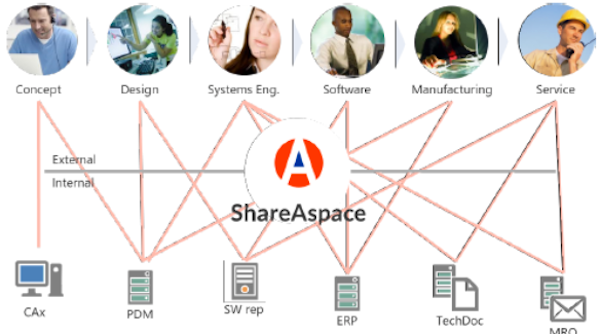
Figure 2—ShareAspace Enables Broad-Based Collaboration (Courtesy of Eurostep)
Their global customers include many familiar names from industries that design, build, and maintain some of the world’s most complex products. Aerospace and defense organizations like BAE Systems, the French Army, Swedish Defence Material Administration, Kongsberg, and Saab rely on ShareAspace for helping to manage IP sharing across global value chains. Automotive customers include Scania, Renault, Volvo Cars, and Volvo Trucks.
Siemens Energy uses ShareAspace for collaboration between Siemens and hundreds of suppliers, both small and large. At Renault, ShareAspace is used to transfer full digital mock-ups (DMUs) between Renault and Nissan. BAE Systems Maritime/United Kingdom Ministry of Defence is using ShareAspace as a repository for all data related to operations and maintenance for new aircraft carriers in the UK. This repository includes imported data creating a digital thread that spans the early phases of the digital thread in design, manufacturing, and integrated logistics support (ILS).
As stated previously, companies are looking to the cloud to better enable collaboration including the capability to be up and running on short notice. The leading PLM solution providers have been slow to move to the cloud, but CIMdata reports increasing interest in that deployment option and some growth in revenues. Most of the leading PLM solutions providers are promoting and supporting a hybrid solution, where some functionality remains on-premise, often engineering work-in-process management, and other workload and use cases around business process collaboration are enabled in the cloud. Small and medium sized enterprises (SMEs) looking to adopt a PLM strategy often look to the cloud because of the ease of deployment. But even these firms may end up pursuing hybrid strategies just because there is so much on-premise legacy IP that will continue to be used.
But the picture is somewhat different when it comes to external data sharing and exchange. Many companies are relying on simple offerings like email, Dropbox, Boxx, or Microsoft SharePoint to share intellectual property. This approach can work for simple file exchange, but these offerings are not built to support product data exchange or sharing. They also were not built with an understanding of bills of material (BOMs), product data standards, versioning and revisioning, and fine-grained security. This makes it difficult to use them to support more complex interactions.
To fill this gap, Eurostep began investing in a cloud-based ShareAspace offering in early 2019. A broad-based survey on current product data sharing and collaboration helped supplement their experience from the on-premise version of ShareAspace. As with many software development efforts, Eurostep is operating an active beta testing program with several lead customers.
ShareAspace Design to Manufacturing targets smaller companies that are suppliers to OEMs. They have the same needs as their larger partners but may not have the skills and resources to implement the more complex PLM offerings relied upon by OEMs. The cloud service is based on the ShareAspace platform and Microsoft Azure.
ShareAspace Design to Manufacturing has several high-level design goals. First and foremost, the service should be as easy to use as possible while still delivering value. It will not allow for customization, one of the downfalls of many PLM implementations, but will support limited configuration. Eurostep will offer something that is “Dropbox-like” but that goes beyond mere file sharing. Their initial offering focus on the Build to Print process. This emphasis makes perfect sense given their SME targets. Suppliers today can get the necessary IP in many ways, from paper to PDF, from native file to lightweight visualization, Excel files, and everything in between. You can’t make the right part at the right time without the right IP. Using a collaboration space in the cloud helps ensure suppliers can and will access the right data. It also makes it possible to share more complex information as shown in Figure 3. The OEMs can push the right data to ShareAspace to ensure suppliers are building to the right “print” and the suppliers can suggest and push change requests back to the OEM.
The focus is on exchanging information to support manufacturing planning, as shown in Figure 3. Many companies rely on 3DPDF to create such technical data packages but Eurostep’s approach supports more dynamism and complex data types. More importantly, it also helps manage any changes to the data, such as change requests and change orders, that result from interactions between design and manufacturing with business partners.
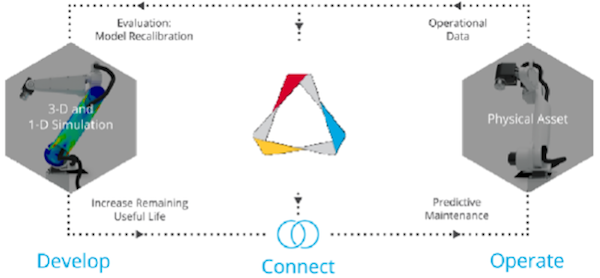
Figure 3—Sharing Complex Work Packages with Manufacturing Partners (Courtesy of Eurostep)
One of Eurostep’s cloud solution launch customers is Weda AB, a Swedish company with fewer than 10 employees. Weda designs and manufactures pool cleaning robots. While this may sound simple it is actually quite complex. These robots also support more complex operations like cleaning water cooling tanks in nuclear plants. By using Eurostep’s cloud solution, Weda claims they will have a much better, flexible, and controlled way to address any issues and changes with supplier components. It also makes it possible to invite Weda staff and suppliers to review and work on the same data in collaborative sessions. It makes it easy for Weda to share the same data with several suppliers, giving them a traceable data set to be shared in a controlled way without impeding the process.
CIMdata sees Weda as a good example that illustrates Eurostep’s market proposition: offering complementary ShareAspace SaaS collaboration services for the SME market. This solution would also work well for niche processes in large enterprises. Eurostep is well-positioned to deliver these cloud-based ShareAspace offerings to this segment, all based on the ShareAspace platform, a sound and market proven technology. While their plans are more expansive, this initial ShareAspace Design to Manufacturing/Build to Print offering fills an important need that helps ensure the right product gets made at the right time. Eurostep is hoping to mimic the success of ShareAspace on-premise and this focused offering ably fills that market need.
Conclusion
Today’s global value chains are getting increasingly dynamic and complex. Intellectual propriety (IP) is the life blood of these collaborations, and companies need secure ways to power data exchange and collaboration across geography, process, and data type. CIMdata has witnessed the success of
ShareAspace in international markets and in supporting value chains for complex products. Their experience in addressing these problems have guided their product development and has served them well with their OEM-oriented clientele.
CIMdata believes this will also serve them well in meeting the needs of smaller companies around value chain collaboration and manufacturing. SMEs have similar needs to their OEM partners but fewer resources to deploy collaboration solutions. In fact, they might not even have an inhouse PDM or PLM system but still need to collaborate with their suppliers. ShareAspace for Design to Manufacturing nicely fills the gap for IP sharing and collaboration. The initial release is due in the Q4 of 2019 and CIMdata looks forward to seeing how this solution evolves to empower design and manufacturing SMEs in their value chain collaboration and digitalization journey.
(1) https://www.edibasics.com/edi-by-industry/the-automotive-industry
(2) http://www.ap242.org/welcome
(3) http://www.plcs-resources.org/ap239/