Key takeaways:
- Experts collaborate better when contextually connected.
- Design changes are completed faster when assembly and requirements traceability is easy to access and examine.
- Reuse of everything, from requirements, to features, to designs, to services, will delight customers with robust products and services.
- Managing product line variations consistently for requirements, features, parts, and subsystems enables powerful reuse, which in turn enhances product and service quality.
- Siemens’ Software & Systems Engineering (SSE) Connected Engineering capabilities provides an integrated, heterogeneous Model-Based Systems Engineering (MBSE) environment managing reuse of everything.
Need to Improve Collaboration Amongst Disciplines
Historically, companies established synchronization points, aka mockups, to assemble a product prototype, first physically and now virtually, to make sure the integrated product will work as intended. A synchronization point is a product context, well-defined, at a particular point of time. This encouraged collaboration to solve product integration challenges, as well as to resolve validation test failures.
Features evolve from one discipline to another as technology evolves. For instance, product usage reveals new load cases to consider and manage. All the buzz about digital twins is about stable configurations of a product to encourage collaborative investigation, evaluation, and decision making. The digital twin for a decision must comprehend the appropriate usage context even if they come after mass production. Discipline experts in software, electronics, and mechanical engineering will use these “understanding-models” to improve their designs. Ideally, they will do this in a user experience (e.g., visualization) and context with which they already are familiar.
Traversing the silos between mechanical, electrical, software, and even systems is ever more challenging as vehicle product and service complexities increase. The frequency of product upgrades is faster as more features are realized in upgradable software systems. Engineering skills are broadening beyond the discipline in which the engineers were originally trained. Computer-based engineering tools have evolved within disciplines but exchanges of information across disciplines has too often been manual and file based. Ultimately, collaboration amongst disciplines must accelerate while also being error free.
The order of decisions needing to be made changes as feature management and reuse of anything are contemplated. The order of decisions is best decided by experts collaborating across the disciplines. Increasing complexity will be handled by more frequent decision points—in fact, it would be best if product mockups were continuous. For that to happen, advances are needed in skills and connected engineering. Principles of agile development and the speed of delivering high quality product features continuously are coming to the forefront. These advances are both in the practices engineers use and in the tools they rely on. Administrative chores for exchanging data should be replaced by computer automation, providing reliable digital twins. Accelerating collaboration is a competitive consideration that PLM solution providers must address. Collaboration must provide reliable context, a trusted digital twin, and insights across multi-disciplines in ways that enable useful decisions in the engineer’s specific domain.
For years, CIMdata has defined and encouraged industry leaders to embrace a systems-of-systems mindset and the need for a comprehensive and integrated PLM ecosystem to help manage it all. PLM is needed for the complete lifecycle comprehending reuse, field upgrades, and even disposal. The PLM ecosystem will have many applications, likely from different solution providers. Connecting tools to enable connected engineering is paramount.
Furthermore, modeling future vehicles with their applications will require improved tools, seamlessly connected. In fact, more disciplines will use understanding-models to answer the question: “Will our existing products in customers’ hands work with the new feature?”
Connected Engineering—Continuous Collaboration
Being able to explore the effects of a proposed change improves product robustness. Reviews for choosing amongst alternatives will accelerate and improve as all disciplines interact together with models. Model-based engineering (MBE) is enabling organizations to transform from serial processes to agile continuous processes. Engineers will be connected all the time rather than just at infrequent, expensive physical mockups. Figure 1 illustrates this fundamental shift driving organizations to rethink their product development processes taking advantage of collaborative understanding-models.
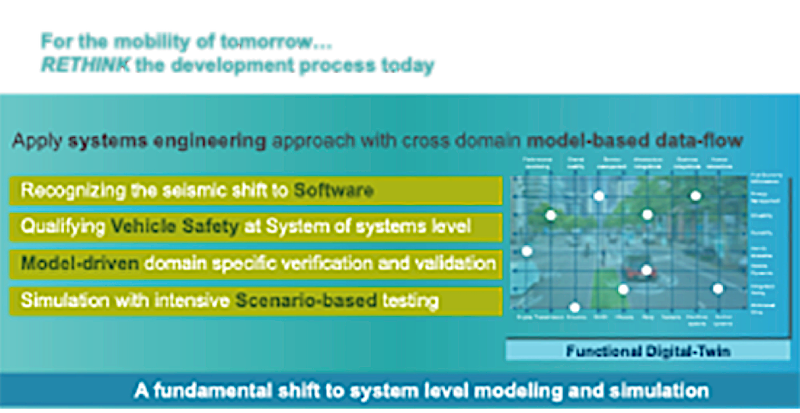
Figure 1—Model-Based Approaches Bridge Disciplines
(Courtesy of Siemens)
The models and tools to assemble, create, share, and record engineering decisions need collaboration via a managed, comprehensive, and end-to-end lifecycle context. Collaboration is complete and trusted when each expert in their discipline can comprehend the effect of the changes being considered. This requires tool bridges that use the same virtual context building trust and confidence. These contexts need to happen on demand, well-orchestrated across the disciplines.
A “systems understanding” framework needs PLM integrated with MBSE to provide interactive views for authors, investigators, and decision makers. Defining a vehicle, assessing it continuously, and re-defining it as usage occurs is the focus of Siemens Digital Industries Software’s (Siemens) Software & Systems Engineering (SSE) portfolio of solutions. SSEs Connected Engineering provides the PLM framework that makes continuous collaboration possible by providing traceability of key items, including test cases, features, requirements, parts, assemblies, and all the rest.
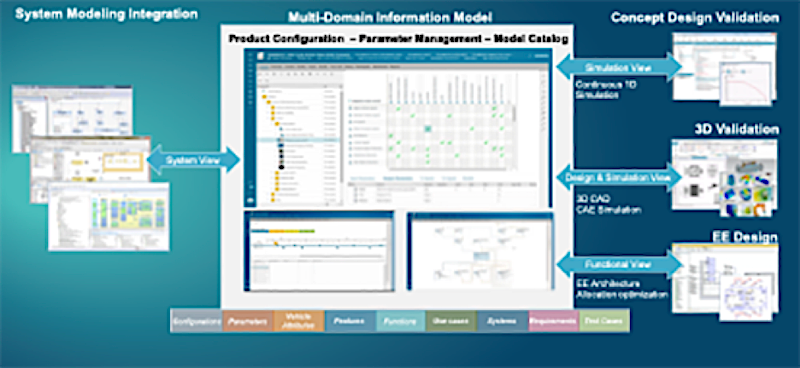
Figure 2—SSE Connected Engineering Multi-Domain Information Model
(Courtesy of Siemens)
Siemens’ SSE Connected Engineering addresses the Multi-Domain Information Model challenges as summarized in Figure 2. Note the items consistently managed for all disciplines, both left and right in the image. Also note the inherent traceability from one item to another.
By managing features instead of parts and assemblies, a clearer measure of customer value is understood across the complete lifecycle. New items being managed directly in the information model allows for better traceability. As engineers work simultaneously, they can examine linkages to other items they depend on in their familiar and context-based user experience. Siemens’ SSE Connected Engineering has coined this capability as exploring “suspect links”— items changing that you care about because they are connected to your item. No more waiting until the next synchronization point due to the information silos not being connected. Engineers are empowered with traceability and contextual/situational awareness, which in turn improves time-to-value and quality, in tandem.
Additionally, Siemens’ Product Configurator solution enables on-demand comprehensive digital twins—accessible and always accurate. CIMdata has commented previously on Siemens’ consistent Product Configurator use within the electrical development ecosystem, Capital.[1] Connected Engineering (using the same Product Configurator) with the advance of suspect links (i.e., what might be changing in other domains and disciplines) will improve robust interactive decision making.
Siemens’ advancements on the way to integrated MBSE are enabling open ecosystems allowing external tools and data sources to be seamlessly integrated. Their partnerships with SAP and IBM[2] are concrete examples for integrating those solution providers’ key tools for logistics and requirements management into a connected engineering ecosystem. Note the API and OSLC technologies depicted in Figure 3. Independent firms like Sodius and SBE Vision are effectively demonstrating OLSC integrations,[3] including the proper exchange of a known context—the product configuration. They can do this because Siemens has integration technologies that foster connected engineering.
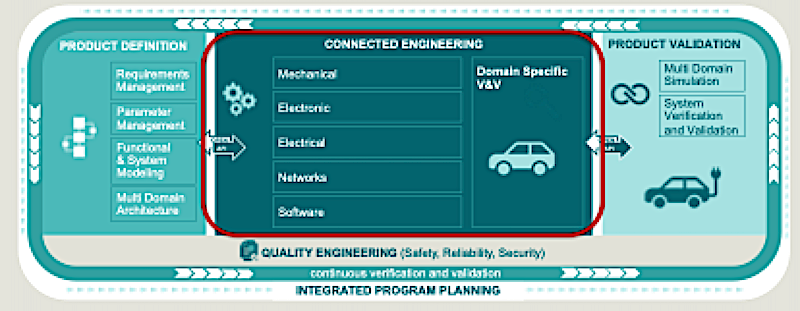
Figure 3—Software & Systems Engineering Pillars
Courtesy of Siemens)
Summary
Systems Engineering practiced by more than experts is a competitive advantage, and when enabled correctly, product and process innovation is enhanced with contextual collaboration. Furthermore, the combination of integrated MBSE tools with reliable vehicle configuration enables a comprehensive digital twin, always accurate to the latest discoveries. To support this, Siemens’ multi-domain information model has been designed to continuously connect engineers by providing an accurate digital twin of the vehicle design, its manufacturing, and its use.
Siemens’ SSE Connected Engineering services are being used today within their Capital suite of solutions. CIMdata recommends that companies consider Siemens’ SSE portfolio of solutions, especially Connected Engineering, when evaluating and/or migrating current vehicle development solutions. With computers and their associated electronics being pervasive, a comprehensive, integrated yet heterogeneous, and multi-disciplinary product development environment is essential in the vehicle development industry.
Siemens’ SSE pillars of Product Definition and Connected Engineering have been summarized in multiple CIMdata commentaries. CIMdata will elaborate on the remaining pillars of the Siemens SSE capabilities early in 2021, see Figure 3.
[1] See: https://www.cimdata.com/en/resources/complimentary-reports-research/commentaries/item/14411-capital-expansion-addresses-e-e-systems-complexity-commentary
2] See: https://process-insights.us/wp-content/uploads/2020/11/2020_Insights_US_IBM_Siemens_Hillhouse_Mantsch.pdf
[3] See: https://www.cimdata.com/en/resources/complimentary-reports-research/commentaries/item/14477-empowering-digital-threads-commentary