Key takeaways:
- Interacting with simulations to improve understanding is moving beyond simulation & analysis specialists to include other engineers, and even product development leadership.
- Pervasive product-use sensing is improving models, which are now being used after mass production to identify quality issues much earlier.
- Scale of possible verification & validation scenarios are exploding—resulting in the is need for an environment to create, manage, and coordinate test cases in specific domains of interest in support of new and existing Automotive engineering activities.
- Siemens Digital Industries Software’s (Siemens) SSE Product Validation offers solutions for managing simulations and test cases needed to cost effectively validate automotive systems, despite their growing complexity.
Managing Simulations Improves Understanding
Models of systems help engineers make informed decisions before committing resources to building a prototype, which is slow and often expensive. These models are used inside simulations to explore how a new system might perform. Simulations are compared to physical measurements, whenever they are obtained. As the limits of a model and its corresponding simulations are understood, often new simulation methods and models are developed to improve the correlation with physical reality. For decades, these simulations have been developed and used by simulation & analysis (S&A) experts with expertise in numerical methods and correlation techniques. They managed the simulations as they improved, often just utilizing file sharing mechanisms within their department.
System Engineering (SE) improves with dynamic assessments of physical/cyber systems—both virtually and physically with the most recent, actual customer’s usages. Simulations can then be used for system robustness assessments by expanding test scenarios beyond the targeted performance envelope to find design weaknesses. As simulation confidence rises, it will increasingly be used for product validation. Replacing physical validation with virtual validation has clear time-to-market benefits. While all final physical validation may not be replaced, doing some validation earlier and continuously will help companies accelerate without compromising quality. Product quality might even improve as phenomena beyond the limits of physical evaluation are explored.
No doubt product complexity will continue to grow and change as products contain more embedded computers. Yet these products come with greatly improved sensing ability, which is being shared in real-time with operations databases, helping traffic control and product service. Consider the OnStar diagnostics report from a vehicle that provided an early example of product sensing of its operational conditions and providing them back to service organizations via a cell phone connection.
For years, CIMdata has defined and encouraged industry leaders to embrace a systems-of-systems mindset and the associated need for a comprehensive and integrated PLM ecosystem to help manage it all, including simulations. Simulation has been used piece meal across PLM, often by phenomena experts. Some of the best original simulation experts were talented test engineers from a laboratory. They understood the limits of measuring and the importance on confirming results with reality.
Simulation can be used throughout the lifecycle and in fact will need to be used a lot more as systems become more complex. The role of managed simulations will evolve into a platform of understanding updated and used daily to assess evolving designs as they are developed by engineering. Simulations will be used to assess operational anomalies to understand whether an emerging field issue might be the bud of a quality problem. More engineers, many not simulation experts, will use simulations to explore failures and missed performance objectives improving their overall understanding of how the product will react in customers’ hands.
What is needed is a simulation platform that makes understanding easier to obtain from the digital engineering artifacts: models, simulations, load cases, and even confidence factors. Improving understanding with simulations makes better products. All engineers, covering all disciplines, will use understanding-models to answer the question: “Will our existing products in our customers’ hands work with the proposed new feature?”
Siemens’ Product Validation Brings Simulation Driven Exploration
Being able to explore the effects of a proposed change improves product robustness. Reviews for choosing amongst alternatives will accelerate and improve as all disciplines interact together with models. Model-Based Engineering (MBE) is enabling organizations to transform from serial processes to continuously executed agile processes. Engineers will be connected all the time rather than just at infrequent, expensive physical mockups. Figure 1 illustrates this fundamental shift driving organizations to rethink their product development processes taking advantage of collaborative understanding-models. Simulations and the boundary load cases of interest need to be professionally managed.
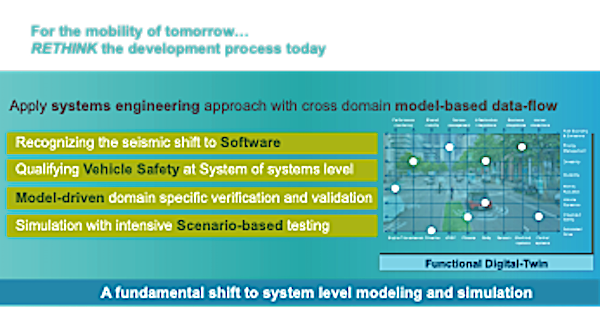
Figure 1—Model-Based Approaches Bridge Disciplines (Courtesy of Siemens)
Collaboration is complete and trusted when each expert, in their disciplinary context, can comprehend the behavioral effect of the changes being considered. This requires a broader simulation management solution that enables building trust and confidence. Simulation animations need to happen on demand, well-orchestrated across the disciplines.
By managing features instead of parts and assemblies, a clearer measure of customer value is understood across the complete lifecycle. Simulations reveal behavior of features under different loading conditions. Imagine a confidence measure of feature robustness to future upgrades. What are the feature implementation weaknesses that might fail later in the product’s life? This is like understanding material fatigue in a product used for thousands of miles. Features supported by embedded software might have sensors that wear out. But they also have susceptibility to future changes and cyber threats. Applying the appropriate simulations let us explore the limits of a design thus building confidence in its robustness.
A “systems understanding” framework needs PLM integrated with Model-Based Systems Engineering (MBSE) to provide interactive views for authors, investigators, and decision makers. Figure 2 is a view of a framework that improves understanding earlier in a product’s life with more of the engineers continuously improving their understandings.
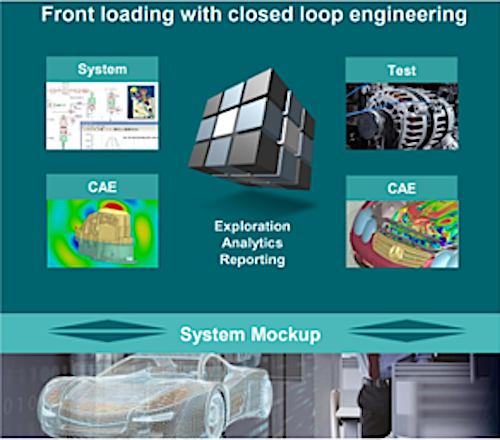
Figure 2—SSE Product Validation Framework Allows Continuous Assessments (Courtesy of Siemens)
Assessing a vehicle continuously and re-defining it as usage occurs is the focus of Siemens’ Software & Systems Engineering (SSE) Product Validation offering. It builds on Siemens expertise of managing simulations and expands into creating and then managing test cases (i.e., scenarios under different environmental conditions) all while providing a user interface for the non-simulation manager or engineer.
“Democratization” of Vehicle Systems Modeling & Simulation
Enabling all people from design, simulation, manufacturing, and service to seamlessly leverage advanced simulations throughout the entire vehicle lifecycle has been the Holy Grail since the first CAD-embedded simulation tools were launched in the early 1990s. The journey has been long and arduous with several false starts and dead ends but now, thanks to the widespread availability of vastly expanded computing and 3D graphics capabilities, the engineering domain is beginning to realize the benefits of this quest. Moving the impact of simulation, stochastic analysis, and optimization activities earlier in the product development lifecycle to meet product performance requirements prior to hardware build and embedded software commitments enables engineers to design more cost efficient, durable, and safe products.
This democratization is now not limited to merely embedding “simpler” analysis capabilities inside mechanical CAD tools. It provides the ability to interact with large-scale physics simulation results across engineering disciplines (i.e., stress/durability, CFD/flow, thermal, etc.) and at varying levels of fidelity (e.g., 0D/1D, 2D, 3D) in both the time and frequency domains. Experienced computer-aided design and systems simulation analysts can define, validate, and encapsulate simulation best practices in easy-to-use applications that can be customized to the needs and level of detail of the intended user. These desktop-based and/or web-deployable tools can safely leverage the power and sophistication of many types of advanced simulation capabilities for 3D parts, sub-systems, as well as systems. Many types of users can be guided through the types of simulations that have been designated as valid Verification & Validation (V&V) best practices by the engineering experts within their own companies. It is a continuously updating, closed-loop platform that speeds understanding, see Figure 3.
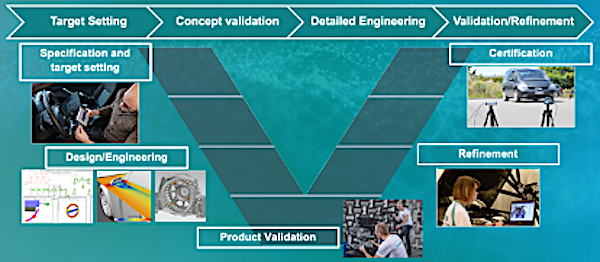
Figure 3—Integrating Physical Testing with Virtual Simulation (Courtesy of Siemens)
Conclusion
Systems engineering practiced by more than simulation and modeling experts is a competitive advantage. The same proven S&A capabilities that have long been used in the automotive industry to validate designs versus physical prototypes can now be applied up front to predict system behavior and to optimize designs versus end user requirements based on key performance indicators. Historically, in-house developed systems and practices have been used by automotive OEMs to manage these activities enabled by custom IT solutions and semi-manual processes. But the complexity of today’s cyber-physical systems, such as hybrid and electric powertrains and autonomously operated vehicles, now require an elevated level of multi-domain systems modeling and simulation that spans software, mechanical, sensors, networking, and electrical engineering domains. It even includes the customer interaction with both the vehicle and its operating environment (i.e., a system of systems approach).
As such, product V&V now needs to start at the systems level in the requirements definition of a new vehicle program and be a continuous cross-domain process throughout the product lifecycle. Such an approach must integrate and optimize the design of systems, sub-systems, and parts to achieve desired user features as well as meet engineering and business requirements in terms of time to profit, R&D cost, durability/warranty commitments and global regulations for safety, natural resource consumption, and environmental sustainability.
CIMdata believes that Siemens provides such an integrated cross-domain and multi-level product V&V framework and simulation capabilities suite that can meet these demanding automotive industry issues at the systems level for cyber-physical product development—from the chip level (i.e., for System-on-Chip (SoC) design using V&V with vehicle systems level scenarios), system level (e.g., advanced driver-assistance systems (ADAS) feature V&V), to vehicle level (e.g., crash and occupant safety), to City level (e.g., virtual V&V for real-world driving scenarios with high fidelity city maps) using virtual-HiL testing of a physical vehicle test-driving on a test track across a range of simulated real world scenarios. Siemens’ SSE Product Validation provides an accurate behavioral digital twin of the vehicle design experiencing real world conditions and loads.
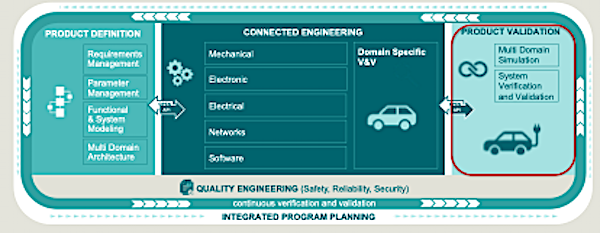
Figure 4—Software & Systems Engineering Pillars (Courtesy of Siemens)
Siemens’ SSE pillars for Product Definition, Connected Engineering, and now Product Validation have been summarized in multiple CIMdata commentaries. CIMdata will elaborate on the remaining pillars, Quality Engineering and Integrated Program Planning, early in 2021, see Figure 4.