Closed-Loop Quality Solution Leverages Teamcenter Backbone
Key takeaways:
- Quality Management Systems must expand beyond a narrow focus of managing manufacturing repeatability and customer usage complaints. Exploring quality from the very start of a new idea, in the context of a trusted digital twin which comprehends changing consumer usage patterns and evolving manufacturing practices, will be the hallmark of leading products companies.
- As product complexity continues to expand, organizations will need quality management techniques applied across the complete lifecycle–this will require organizations to redefine roles and governance within PLM in the context of product lifecycle quality.
- Siemens Teamcenter enables the digital thread and management of product data flowing across the complete lifecycle supporting closed-loop quality and comprehensive digital twins.
- Siemens is introducing a set of Quality Management capabilities built upon Teamcenter’s lifecycle collaboration backbone solution including defining and managing a Bill of Quality.
CIMdata’s definition of PLM emphasizes the complete lifecycle of a product and all its related data, from requirements to actual performance, to planning, with supply chains, and then mass production and product upgrades. Quality Management Systems (QMS) have historically focused on manufacturing products consistently and improving product durability. Imagine applying QMS practices to all parts of an organization developing and operating products. The techniques of quality management can be applied to engineering processes, manufacturing processes, supplier processes, and even discoveries in new markets. Their use improves as PLM systems have enabled an accurate digital twin throughout the lifecycle.
As product complexity increases and with new and expanded features even being delivered while a product is in-service, a more expansive use of quality analysis methods is required. This comprehensive quality management paradigm assures product quality is earning the trust of customers and the OEM is rewarded with higher sales volumes and brand loyalty. This is broader than the notion of classical quality management systems using their own process and data silo applying statistical process control as though every manufactured item is a black box to be studied as a population of samples.
Expansion of Quality Management Responsibilities
Modern PLM ecosystems are well positioned to foster a Quality Management environment throughout the product lifecycle. Applying systems engineering (SE) principles anywhere in the lifecycle requires a quality management mindset where anomalies uncovered in FMEA, inspections, or complaints can be immediately evaluated with models and newly discovered use cases. Model-based quality management allows variation analysis to be digitally validated earlier in the product development process. Creating and sustaining an actionable, living digital twin annotated with failure insights and design/supplier weaknesses improves product quality management. Containment as well as preventive measures then become a pervasive, even natural, part of the engineering, manufacturing, and customer service processes. By using a digital twin, even supply chain improvements can be immediate with integrated quality management practices. The digital twin is used more and more to assess operational anomalies to understand whether an emerging field issue might be the bud of a quality problem.
At Siemens’ Realize LIVE 2021 conference, Mr. Brian Sniegocki, Senior Business Analyst at Dana Corporation, presented his vision of how collaboration enables closed-loop manufacturing. To improve collaboration, one must integrate FMEA with CAD models with quality reports, across a product’s lifecycle from inception through operations. He discussed how a broader quality management framework with effective data governance enables collaboration between various roles during each phase: planning, execution, manufacturing, and service.
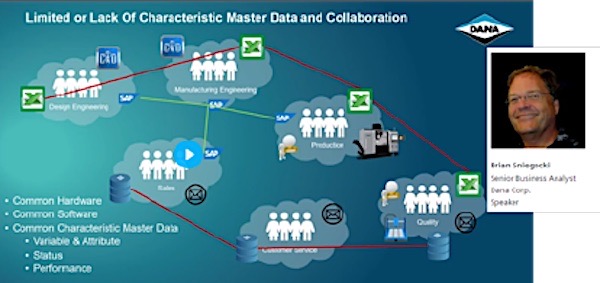
Figure 1—Too Many Silos / Documents Limit Data Collaboration
(Courtesy of Dana Corp)
Figure 1 describes capturing the breadth and integration needs for key Quality and Systems Engineering (SE) work products. No more e-mailing electronic documents, rather have the information presented in the context of a product bill of materials (BoM) and a manufacturing bill of process (BoP).
To support this vision, a digital twin must be available on demand and accurate to the latest customer usage patterns. Many work products have traditionally been managed in separate IT systems, often with bespoke user interfaces tuned for authors, not readers and researchers. A digital transformation is needed to connect these work products well by having consistent product terminology. Master Data governance is an organizational best practice that provides a single dictionary for product, manufacturing, and operating terminology.
Competitive and complexity pressures require faster decisions made well. SE, Design for Six Sigma (DFSS), and design thinking are all skills which practicing engineers must embrace, regardless of their domain of expertise. Product requirements are best managed in a repository containing the authoritative truth that enables different views and analyses as product lines are conceived and enhanced. A bill of requirements (BoR) should be managed like a BoM, as part of the product’s Bill of Information (BoI). The BoI is inclusive of all information related to a product covering its whole lifecycle.
By bringing model-based quality to reality, imagine doing variation analysis on digitally validated CMM / Inspection programing as part of dimensional planning and validation. With a capable PLM system, the designer can interactively see the effect of design choices on manufacturing’s inspection BoP. Quality Management becomes closed loop all the time, even providing field insights as customers use products.
Modern PLM systems must not only manage these work products Mr. Sniegocki noted, but they also need to make finding and organizing views of the information more convenient than in the past siloed IT systems. His point is shared by most PLM leaders CIMdata has worked with. A Bill of Quality (BoQ) which is lifecycle wide and seamlessly and continuously aligned with the BoM, BoR, BoP, and BoI is needed.
Siemens Quality Management Solution Enables Lifecycle Bill of Quality
Siemens Quality Management Solutions will help customers bridge gaps between roles and work products which in turn improves collaboration. Siemens defines a Bill of Quality as shown in Figure 2.
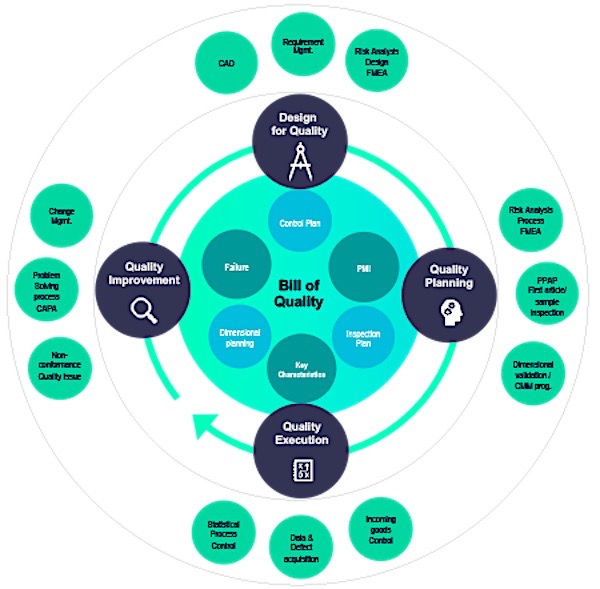
Figure 2—Bill of Quality Encompasses the Complete Lifecycle
(Courtesy of Siemens)
Siemens recognizes that quality management’s value must extended beyond production to all core business processes for all product domains. This means breaking down diverse data silos (and allow for re-engineering the organization), providing a capable and flexible work product repository assisting complexity management, data sharing, and configuration management.
Figure 3 illustrates an extended architectural landscape to encourage Closed-Loop Quality, including ERP, PLM, and MES systems. Note how the swim lanes interact with the digital twin, which becomes elaborated with quality specifications and measures throughout the lifecycle.
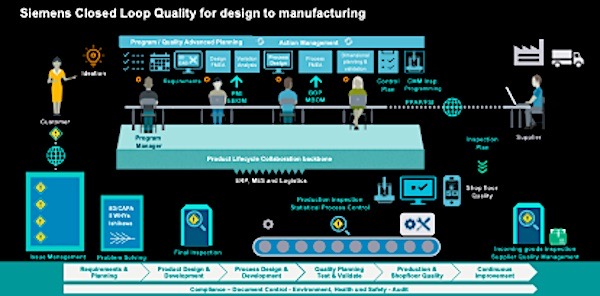
Figure 3—Product Lifecycle Collaboration to Support Closed-Loop Quality
(Courtesy of Siemens)
It utilizes Teamcenter to provide a Product Lifecycle Collaboration backbone. Using Siemens Mendix technology for open-systems integration with legacy (often competitive advantage) systems, the platform expands as the digital twin model(s) are used everywhere. Closed-Loop Quality broadens the domain of quality management to the complete closed-loop lifecycle of products.
Siemens Quality Management Solution Accelerates PDCA
Another view shared at Realize LIVE 2021 was a persistent, continuous feedback loop, as taught by Dr. Edward Deming, using Plan-Do-Check-Act (PDCA[1]. Learning and feedback to proactively repair and enhance products is driven by the Plan-Do-Check-Act cycles. An annotated digital twin provides context of the insights making Planning easier. Do & Check occur interactively with the model allowing Act to successfully proceed.
To address the master data integration challenges Siemens’ holistic vision for quality management systems has adopted the PDCA paradigm applying it to connect key work products in the context of discovery and then application of lessons learned. The cycles are repeated until a solution is found and can traverse to early work products wherever the problematic conditions started. This leads to a holistic view of quality management rather than just a mass production view.
Data integration across formerly siloed applications is a key to success for streamlining quality management and keeping it “closed-loop” with continuous, contextual feedback encouraging a culture of quality within a company’s value streams. Configuration and change collaboration within this continuous feedback loop will provide full traceability, making quality management more proactive than reactive, and thus much faster.
This holistic quality view improves systems designs for the entire lifecycle, rather than just stopping at manufacturing. Making sure products when placed in initial service and when upgraded perform better by leveraging digital twins and the digital thread. Figure 4 shows how Siemens integrates the PDCA cycles encouraging a holistic quality view.
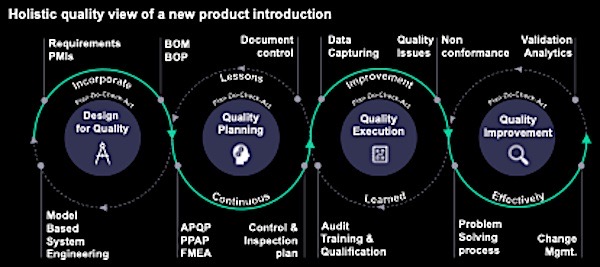
Figure 4—Holistic Bill of Quality Encompasses Complete Lifecycle
(Courtesy of Siemens)
The notion of the expanding Agile development’s DevOps[2] into interconnected infinity cycles helps shift the mental model to one in which quality insights build trust continuously across the life cycle. As new field / phenomena results are captured, models and their simulations are improved, and quality risks and learnings are explored. It incorporates lessons continuously through improvements learned effectively.
Concluding Remarks
Siemens Quality Management Solution provides a foundation to address the quality data integration and collaboration challenges laid out by key customers. CIMdata forecasts that companies connecting data well can realize significant productivity benefits using Siemens Quality Management Solutions.[3]
Setting a vision with this new Quality Management solution, Siemens customers will soon see benefits. Mr. Paul Elvinger, Executive Board member at Cebi says, “An important aspect in our digital transformation is to set up a common approach for managing product information and improve collaboration across Cebi’s global network, in which all actors bring their added value to meet customer expectations in terms of product innovation and quality.”[4]
This is what happens when the leading solution providers build on their strengths—in Siemens’ case their Xcelerator platform with Teamcenter as the collaboration and data management backbone, and openness to enable customers to accelerate learning and enhancement cycles. The Teamcenter backbone leverages low code (i.e., Mendix) services to encourage domain specialists to become citizen application developers-easing IT’s burden and systems integration challenges. With Mendix you can personalize your application user interface tailored to your business processes without limiting yourself to future system upgrades.
Finally, holistic Quality Management encourages linkages between silos of experts and their knowledge, driven by data. Too often silos remain when experts want to have their “way of working” explicitly supported in commercial tools, which was historically done in legacy bespoke applications. A required similar user experience is often the Achilles heel to broader quality management practices. Siemens QMS will provide another reason to embrace comprehensive digital twins.
[1] https://en.wikipedia.org/wiki/PDCA
[2] https://en.wikipedia.org/wiki/DevOps
[3] https://www.plm.automation.siemens.com/global/en/series/siemens-quality-management-in-the-digital-era/99575
[4] https://www.plm.automation.siemens.com/global/en/our-story/newsroom/teamcenter-quality-enterprise-wide-quality-management/93227/