In a recent briefing to CIMdata, Siemens Digital Industries Software[1] showcased technical innovations that enable customers to create and leverage an executable digital twin (xDT[2]). An xDT is a smart, connected virtual representation of a physical asset, including its behaviors, that senses what is happening to it, applies a simulation or algorithm, and then optimizes and updates itself. It processes sensor information (at the edge or in the cloud) to recognize its environment and then adjusts to those conditions. CIMdata sees this innovation as a milestone in product design, production, and usage, by taking what has, to date, only been a virtual copy of a product’s geometry to a working model that can facilitate autonomous adjustments of the product within its actual operating environment and use across its lifecycle.
Physical testing is, in most cases, still integral to making sure simulated virtual models accurately predict what really happens. By having reduced order models adapt to measured data, often in real-time, and then seeing the physical effects with visualization techniques, engineers will be able to make design improvements faster. Siemens provided several examples of how an xDT can deliver feedback that can be used to improve design engineering, manufacturing, and the in-service life of a product.
For design, users should gain faster system optimization with model-based system testing using ASAM XiL,[3] measure the unmeasurable with smart, virtual sensors, and better leverage product usage and performance data.
For manufacturing, the technology can be used to help predict production process quality, compensate for gaps in instrumentation with smart, virtual sensors, and de-risk and shorten the commissioning of software and machines. Instructions to the machine (I.e. speed up, slow down, stop, turn) can be executed based on the predictions.
For service, it provides in-the-field smart, model-enabled predictive maintenance and enables collection and smart data reduction for use in both repair and design. Figure 1 highlights using simulation and test with reduced order modeling to create an xDTand then use it in real time.
In addition to in-operation actuation or adjustment, Siemens described using xDTs also as the way to enable “bringing the real world into product design optimization.” They walked through the steps needed to take a product’s standard digital twin, create an xDT within Siemens Simcenter, use laboratory test measurements for model adaptations, and then package and deploy the xDT either in the cloud or on edge devices. Siemens’ xDT advancement is an important step to making models relevant throughout the entire product lifecycle. CIMdata looks forward to the additional and varied use cases Siemens customers create from this advanced technology innovation.
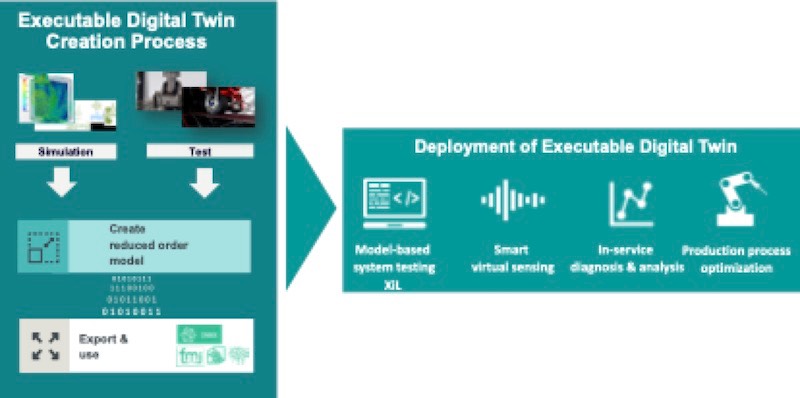
Figure 1—Create and Use an xDT
[1] Research for this commentary was partially supported by Siemens Digital Industries Software.
[2] xDT is a CIMdata shorthand convention for Executable Digital Twin.
[3] ASAM XIL is an API standard for the communication between test automation tools and test benches.