Siemens solutions foster continuous verification and validation
Key takeaways:
- Continuous virtual verification and validation through all phases of the product lifecycle―throughout design, manufacturing, and operations―is critical so that an automaker can assure intended functions from their inception.
- Only a fully integrated solution, that includes virtual integration and simulation capabilities, can enable the process revolutions keeping automakers competitive.
- Digital twins correlated with physical performance test results and virtual evaluations enable continuous collaboration and optimization helping stakeholders across different disciplines concurrently work together as a product evolves.
- Reducing or eliminating early physical prototypes through simulation and linking requirements with test results yields time savings and shortens verification cycles from months to weeks, and in some cases hours. Continuous, visual product assembly and performance motion studies of subassemblies as they are designed provide insights earlier in product development.
- Siemens Digital Industries Software Systems Digitalization solution is designed to keep product development teams integrated, improve decision-making across the lifecycle, and keep relevant requirements visible all the time.
Automakers’ product development is constrained by the time it takes to build physical mockups and samples for development testing, often called learning loops. The challenges associated with evaluating a design using physical prototypes include months of construction and then testing in a laboratory or on a test track. Sometimes prototypes are ideal product representations and do not reflect typical mass manufacturing realities. Time to market and improving quality while introducing new features faster drives the automotive marketplace as summarized in a recent CIMdata whitepaper[1] covering accelerated product development (APD).[2]
CIMdata’s definition of product lifecycle management (PLM) emphasizes the complete lifecycle of a product and all its related data and processes, from requirements to, to planning and supply chain participation, then mass production, actual in-use performance, product service and upgrades, and finally decommissioning and recycling. Systems Engineering accelerates automotive product development and operations by considering this broader context―one that includes the operational environment of the vehicles.
Automotive product development process reengineering must address scheduling, critical path, and material constraints. Systems engineering and advances in inexpensive computing and the use of virtual engineering are challenging the legacy processes automakers use. Collecting and using customer usage patterns to influence product development and upgrades is becoming required to staying competitive. In the APD whitepaper, CIMdata introduced the notion of continuous product performance engineering where test sets can be used to perform verification and validation evaluations on demand. Using virtual integrations enables the reduction of physical prototypes, which in turn allows for faster learning cycles―and likely more of them (the ability to perform more and better design/performance optimization).
Many product development issues are better found through simulation, which only needs a coordinated release of component designs and not the complexity of scheduling and waiting on physical samples. Using simulation to continually evaluate a design, especially the integration of key components and subsystems, without waiting on physical prototypes significantly streamlines critical path activities in automotive product development. Removing this constraint, especially during earlier development phases, allows more features to be introduced faster. Software systems can be evaluated with virtual product models earlier, and then integrated with electronics, wiring, and the rest of the vehicle for final validation testing. Continuous verification and validation of designs, test/simulation results, and product complexity using comprehensive digital twins is possible and essential to stay competitive.
Continuous Learning Drives Constant Verification and Validation
Constant learning during development is key to incorporating new technologies and bringing new features to market. Learning is continuous when the next feature can be evaluated as it is developed rather than months later using a physical prototype. Over the past few decades, virtual mockups have replaced physical bucks for exterior shape and interior ergonomics reviews and software developers have relied on computer-based test environments to evaluate their software behavior and performance. Today, using representative models of physical systems, integration-based evaluations, motion-studies, and even destructive virtual testing to find the limits of a design can be done cost effectively.
Each loop within the automotive ecosystem collects empirical measurements needed to train models and make them trusted. Sensor and actuator models for each subsystem under test provide stimulus and response as if the subsystem were in an actual driving scenario. With trusted models, teams collaborate faster making virtual verification and validation desirable.
Figure 1―Continuous Virtual Verification and Validation Accelerates the Pace of Innovation
(Courtesy of Siemens)
Siemens has identified their solution set for advancing virtual engineering as Continuous Virtual Verification and Validation (CVVV). Figure 1 shows how CVVV encompasses all phases of product development. Depicting it as a cycle of learning that is constantly evaluating designs, emphasizes the continuous nature of learning―best achieved without delays waiting on physical prototypes.
With modern communications and in-vehicle electronics, continuous improvement of automobiles during operations is occurring. Validation of an upgrade must be managed, even as upgrades are occurring more frequently. Assuring safety by applying trusted, shared models that learn from expansive sensing of the vehicle’s operation is now possible. Building trust in virtual models of an operational environment requires constant evaluation of customer real-world scenarios. Automakers rely on learned, complex operational scenarios. This means building models at every layer of abstraction from diverse data silos each containing different empirical insights. Leveraging real-world measurements to correlate virtual model-based scenarios using digital twins to help assess complex operational anomalies will make automotive upgrades safer and more reliable, thereby fostering societal trust. Constant learning and adaptation keep models trustworthy. Doing this in near real-time keeps them well correlated. With correlated models and real-world scenarios, continuous verification and validation is possible.
Performance engineers conduct product level validation tests as one of the final steps before a product is released for mass production. Performance engineering goes beyond verification test suites and includes an assessment of varying operational conditions like weather, velocities, road conditions, friction, and many more. Select validation test cases must be repeated when a vehicle upgrade is made. The event triggering a validation test is different than the mass production launch.
Automating the execution and evaluation of test suites as often as a new feature set is ready will become a competitive advantage over manual and open loop hardware-in-the-loop testing. Orchestrating tests across a wide variety of systems for each incremental change needs effective incremental verification and validation scenario management. Coordination between the levels of testing, from component verification to subsystem and system validation, will benefit automotive product development, likely shortening time to market while improving the quality of design and upgrades.
One last point, teams working collaboratively in parallel while using the same trustworthy models will develop enhancements and/or investigations from different expert contexts. Contexts for decision-making will be improved with automated, continuous verification and validation derived from actual usage patterns, likely derived from real customer experiences. Validation engineering is becoming continuous for automakers, performed whenever a new release is to be provided to the customer.
How Siemens Enables Continuous Virtual Verification and Validation
Siemens recognizes that all core business processes for all product disciplines must perform verification and validation, from components to final systems. Software systems with millions of lines of code rely on automated, daily test suites where anomalies are detected automatically. Quality teams then assess and often adjust the next release, which is provided in a few days, not years. Siemens has embraced the need for continuous collaborative engineering driven by faster product releases and upgrades. Their CVVV suite has capabilities used across the development phases and cycles depicted in Figure 1. By combining capabilities from their broad solution set, Siemens has incorporated testing automation capabilities that span the major engineering domains. Functions from systems engineering to systems interaction to verification and validation are all supported by managing simulation scenarios across the tool suites. Figure 2 summarizes these domains and the broad design & simulation tool suites that support them: Thermal, Topology, Motion, Vibration, and more.
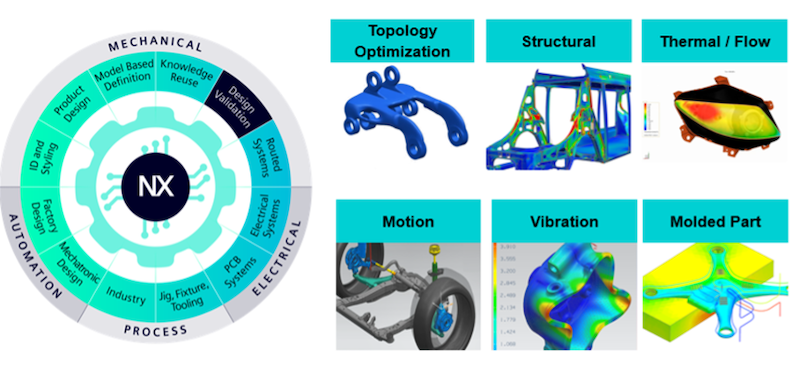
Figure 2―Empowering Designers & Engineers with NX Integrated Simulation Tools
(Courtesy of Siemens)
By combining simulation capabilities within its NX CAD suite, Siemens helps bridge the disciplines noted in Figure 2. Earlier discovery helps accelerate concurrent engineering. CIMdata believes that Siemens concept of Continuous Virtual Verification and Validation executed continuously from Definition to Concept, then Development, and finally Validation, as illustrated in Figure 1, is excellent. By combining key tools from their broad solutions set, including executable, comprehensive digital twins, Siemens is enabling virtual engineering, moving integration and discovery at all levels earlier in the development process. No more waiting on development physical prototypes.
Designers and engineers can now discuss and decide how vibration effects heat transfer and even how structural dynamics effects durability, earlier in the development process, lowering new product risks. Adjusting the automobile controls to manage a post-production discovery helps improve long term product life, keeping it operational. Combined with Auditable Requirements Traceability,[3] these capabilities assure product developers are always using and evaluating the correct set of requirements―even as requirements change during development and use.
Simulations need load cases and related environmental conditions. Siemens has tools for discovering and managing test scenarios as they are experienced―these include Prescan 360 and Simcenter SCAPTOR, summarized in a commentary by CIMdata.[4] Siemens Prescan 360 supports performance testing by synthesizing and running repeatable scenario tests with varying boundary conditions. By using models of sensors and vehicle dynamics, the signals a control system would monitor can be emulated, making the control system react as it would in the final product. This enables control system development independent of physical vehicle integration and evaluation. This means re-validation after mass production becomes affordable, which in turn encourages more post mass production feature introductions.
Simcenter SCAPTOR helps orchestrate newly discovered scenarios which spur expansion of verification and validation criterion. By managing the scenarios needed to cover sufficient verification and validation testing, Simcenter SCAPTOR helps automakers achieve product validation without billions of miles of physical testing―which is a forecast from some automaker executives based on the historical practice with build and break test cycles.
Concluding Remarks
Product engineering has always focused on what customers value―safety, fun, luxury, and lifestyles. The accelerating pace of changing consumer tastes, thus the need to adjust performance measures, will occur at a faster and faster pace. CIMdata forecasts that automakers using Siemens’ CVVV solution set can realize the expansion of virtual, continuous engineering. This virtual engineering growth cannot slow down product development, and with Siemens continuous verification and validation capabilities it will not. Rather the development processes will evolve and the interaction of performance engineering with the other disciplines will accelerate. Comprehensive, efficient product engineering remains a competitive advantage and process innovations will be revolutionary with continuous verification and validation.
Siemens’ CVVV solutions provide test creation and management capabilities for execution and correlation studies at all levels of automotive design and operations, utilizing a combination of local and cloud-based technologies. Continuous verification and validation becomes cost effective when most of it is done virtually. When required, hardware subsystem and integration testing will be done with the same scenarios as those used in the virtual simulations. Siemens’ multi-domain information model has been designed to continuously provide an accurate digital twin of the vehicle throughout its use. Siemens provides a solution set ready for future automotive development and operations―supporting all product upgrades with their SSE, Capital, and now CVVV solutions.
CIMdata recommends that companies evaluating their need for verification and validation consider Siemens’ portfolio of solutions. With computers and their associated electronics being pervasive, a comprehensive, integrated yet heterogeneous, multi-disciplinary product development environment connected to all stakeholders is essential. Siemens’ ongoing advances in Quality Management,[5] Systems Engineering,[6] Simulation with Executable Digital Twins,[7] Connected Engineering,[8] Systems of Systems Frameworks,[9] and future concepts in the works provide a rich set of capabilities. Finally, Siemens is providing engineering tools that can be used to explore operational conditions as they are experienced. This is what happens when a leading solution provider builds on their strengths.
[1] See: Accelerating Product Development (Faster Decisions While Reducing Physical Prototypes). January 2022. https://www.cimdata.com/en/resources/complimentary-reports-research/white-papers
[2] Research for this commentary was partially supported by Siemens Digital Industries Software.
[3] https://www.cimdata.com/en/resources/complimentary-reports-research/commentaries/item/18101-siemens-provides-interactive-auditable-requirements-traceability-accelerating-development-of-complex-automobiles-commentary
[4] https://www.cimdata.com/en/resources/complimentary-reports-research/commentaries/item/18008-siemens-fosters-connectedness-bringing-products-and-cities-together-commentary
[5] https://www.cimdata.com/en/resources/complimentary-reports-research/commentaries/item/16341-a-broad-approach-to-quality-management-commentary
[6] See: Driving the Change for the Future of Automotive Development. 24 November 2020. https://www.cimdata.com/en/resources/complimentary-reports-research/white-papers
[7] https://www.cimdata.com/en/resources/complimentary-reports-research/commentaries/item/16725-siemens-making-the-digital-twin-executable-predictively-aligning-its-real-world-counterpart-highlight
[8] https://www.cimdata.com/en/resources/complimentary-reports-research/commentaries/item/14887-connected-engineering-accelerates-innovation-commentary
[9] https://www.cimdata.com/en/resources/complimentary-reports-research/commentaries/item/17304-siemens-broadens-mbse-to-engineer-beyond-individual-autonomous-vehicles-commentary