Leveraging AI/ML, data analytics, and optmization across the enterprise
Key takeaways:
- Dealing with the design complexity of cyber-physical products and smart, interconnected systems of systems is driving the need for increased use of advanced digital modeling, simulation, and multi-disciplinary analysis and optimization (MDAO) augmented with AI/Machine Learning technologies.
- Engineers can now define and apply multi-disciplinary digital twins and MDAO starting earlier in the conceptual design and development phase as well as apply it in manufacturing and in operations to enable combined physics and ML-based “hybrid digital twins.”
- Industry leaders use MDAO to enable design innovation; reduce overall product design costs, minimize rework and manufacturing defects, reduce maintenance cycle times, and optimize in-service operational performance and costs.
- The low-code pSeven collaboration environment enables the capture, automation, and continuous refinement of best practices for performance simulation and design optimization to significantly improve overall engineering productivity.
- DATADVANCE pSeven Enterprise leverages company intellectual property in web-based MDAO and data analytics vertical applications used by engineers and data scientists across many technical domains.
- This “democratization” of physics-based modeling, performance simulation, design optimization, and data analytics best practices throughout the enterprise is a key enabler of digital transformation initiatives.
Manufacturers in all industries have been applying digital modeling and simulation technologies since the 1970s but today face new challenges as products continue to become more complex, capable, and connected. As part of the Industry 4.0 “systems of systems” world, products have an ever-increasing amount of embedded software and electronics. To successfully compete in today’s global markets, manufacturing industry leaders must leverage new and evolving technologies to digitalize their lifecycle development processes while maximizing and modernizing existing investments in modeling and simulation. The design and development of complex cyber-physical systems requires well integrated capabilities for cross-disciplinary simulation, analytics, and design optimization including the use of Artificial Intelligence (AI) technologies to enable Machine Learning (ML) and Deep Learning (DL). The promised business benefits of AI/ML/DL have significantly raised the ROI expectations of senior management as the next generation of internet savvy engineers and scientists readily embrace these new technologies.[1]
But domain-specific tools and disjointed development processes do not deliver the connectivity of information required to enable collaborative decision-making across engineering functional disciplines (i.e., mechanical, electrical/electronics, software, etc.) and across enterprise domains (systems engineering, R&D, test/V&V, manufacturing, operations). And the ongoing loss of generational experience and expertise combined with an overall degradation of fundamental engineering skills (i.e., by the TikTok/You Tube generation) increases the need to be able to leverage the skills of expert simulation engineers and data scientists to define and distribute new product design and simulation methods for use by many others (i.e., democratization). Professional engineers and scientists (i.e., experts and power users) must develop, validate, and automate MDAO best practices for use by “domain-specific” engineers who may have limited knowledge of the underlying simulation technologies and related AI/ML data analytics tools.
And with the emergence of IoT platforms and the numerous sensors now applied to in service products, the use of AI/ML and data analytics is taking on an ever increasing role and importance to validate and refine physics-based “hybrid digital twin” models used to predict and optimize the performance of cyber-physical products and manufacturing systems.
DATADVANCE
DATADVANCE is an independent software developer that provides engineering software solutions and consulting services for intelligent design space exploration and predictive modeling. The company is based in Toulouse, France at the heart of European aerospace, and it has more than 10 years of experience working with leading aerospace companies across the globe. Apart from aerospace, typical customers today are in the automotive, life sciences, heavy machinery, ship building, offshore, energy, and turbomachinery industries.
DATADVANCE develops, sells, and supports predictive modeling and design space exploration solutions, packaged into an easy-to-use, low-code, web-based software portfolio called pSeven. DATADVANCE collaborates with leading global software vendors, research centers and universities to continuously innovate and improve their software products and services.
The DATADVANCE pSeven Portfolio
The pSeven portfolio is a suite of MDAO capabilities that can be used independently on an engineering desktop as well as be tightly integrated into an enterprise level Cloud-native workflow automation solution. Figure 1 illustrates the suite of pSeven software solutions.
Figure 1: The pSeven Portfolio
(Courtesy of DATADVANCE)
pSeven Core
pSeven Core is an interconnected set of tools with proprietary, state-of-the-art algorithms for design exploration and predictive modeling packaged as a Python module, the de-facto industry standard for scientific computing. pSeven Core is available standalone or embedded as part of the pSeven suite.
- Users at all levels can perform design space exploration studies leveraging a wide range of pSeven Core capabilities, including efficient and industry proven machine learning, and multi-objective and robust design optimization algorithms.
- Smart Selection―Automated selection and tuning of the “best fit” machine learning and optimization algorithms, implemented in pSeven Core, enables non-expert engineers and data scientists to leverage powerful MDAO tools and predictive analysis capabilities to support hybrid digital twin applications.
pSeven
pSeven creates reusable “best practice” MDAO simulations as well as “hybrid digital twins”―simulations combined with empirical data-driven ML algorithms. pSeven capabilities are available on the engineering desktop or in cloud platforms deployed and operated by the customer’s IT organization.
- Easy to use visual programming to define and automate scalable empirical data analyses and multidisciplinary design optimization workflows.
- Create workflows to orchestrate and automate the execution of various design and simulation tools for product functional performance evaluations created separately by different discipline teams and then assembled into a master workflow without the need for any manual rework and data transfer.
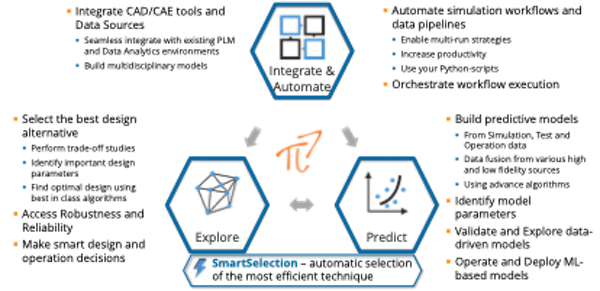
Figure 2: pSeven Enterprise delivers all the pSeven Capabilities in the Cloud for Simulation Automation, Design Exploration, Predictive Analytics, and Collaboration(Courtesy of DATADVANCE)
pSeven Enterprise
pSeven Enterprise is a low-code, cloud-native environment to enable enterprise-wide creation and publishing of engineering MDAO best practices as well as cross domain collaboration by engineers and scientists at all levels of the extended ecosystem.
- Project teams can define, edit, and share multi-disciplinary simulation, design space exploration, and predictive analytics data processing workflows in a common, cloud-native workspace leveraging the same UI and core capabilities contained in the pSeven and pSeven Core desktop applications.
- It provides multiple levels of capabilities designed for different engineering user communities, functional roles, and skill levels:
- Enterprise Studio and Enterprise Analyze for expert and power users.
- Enterprise Apps Hub (a.k.a. enterprise AppStore) for users and consumers of domain specific applications and services, backed by monitoring, orchestration, and automation tools (i.e., democratization).
- It has an open and scalable cloud-native environment:
- Open API enables data interoperability with other collaborative engineering environments such as SPDM, PLM/PDM, ERP, and empirical data from physical assets (through IIoT platforms).
- pSeven Enterprise runs in public and on-premises cloud environments with capabilities such as “fire and forget” to delegate workflow execution to any server with a built-in resource manager.
- Cloud-native architecture enables authoring and exploitation of engineering methods from any network connected device.
pSeven Industrial Application Examples
pSeven has been successfully applied since 2012 across a wide range of industries to enable multi-disciplinary design space exploration and optimization, leveraging simulation workflow automation that integrates a variety of design, simulation, and AI/ML predictive modeling data analysis tools. Some notable customer applications include:
Airbus: Multi-Objective Optimization of Aircraft Family
Objective
- Optimize a family of 3 airplanes at the conceptual design stage to ensure minimal model modification and related costs at later stages.
Challenges
- High dimensionality: 9 objective functions, 12 design variables, 33 non-linear constraints. The optimization problem was considered unmanageable by a human engineer.
Solution
- Gradient-based multi-objective optimization integrating custom in-house simulation tools.
Benefit
- ↑ 5% performance improvement
- ↓ 20% design time reduction
Mitsubishi Motors: Predicting Combustion Model Parameters
Objective
- Predict combustion model parameters for accurate engine modeling.
Challenges
- Fixed number of experimental data elements available
- High accuracy of predictions is required.
Solution
- 1st stage: Fitting combustion parameters to existing experimental in-cylinder pressure vs. crank angle curves using optimization.
- 2nd stage: Creating a model to predict combustion parameters at an arbitrary regime using known values.
Benefit
- Fast and accurate predictive model was created that can be used in further 1D vehicle acoustic simulations via export to FMI.
Concluding Remarks
Real world systems are subjected to a wide range of operating conditions and customer applications; use cases that are often not explicitly accounted for during the design and development process. As such, understanding the impact of design variability on “as manufactured” and “as maintained” product performance is key to employing hybrid digital twins to accurately analyze, predict, and optimize today’s complex products and systems.
In CIMdata’s opinion, the pSeven product portfolio provides an excellent suite of capabilities that enable simulation-driven systems development via effective MDAO process automation and web-based collaboration for product development teams. It also provides robust design exploration capabilities that work across multiple domains in the enterprise such as physics-based digital twins for use in R&D, product design, manufacturing, and in-service operations.
While DATADVANCE is relatively unknown within North America, we expect that situation will change rather quickly as more companies become exposed to the business impact of implementing the pSeven technology and its empowering capabilities.
See www.DATADVANCE.net for more information.
[1] Research for this commentary was partially supported by DATADVANCE.