Industrial operations and maintenance processes facilitated with IoT-enabled smart assets
Key Takeaways
- The usage of Internet of Things (IoT) connected devices in industrial settings is expanding rapidly across many sectors.
- Industrial users of capital assets are benefitting from the use of IoT to improve asset uptime and automate business processes in production and maintenance, repair, and operations/overhaul (MRO).
- Asset manufacturers are also benefiting through the efficient provisioning of smart services to support their customers and by leveraging valuable operational information.
- CONTACT Software has extensive experience in supporting the use of IoT for improving the management of industrial assets.
Introduction
The Industrial Internet of Things (IIoT) connects factory machines and equipment with software services that focus on optimizing manufacturing processes and enabling digital services for smart products. For factory operators, IIoT opens new opportunities for them to monitor usage and improve maintenance processes for their industrial assets. For manufacturers of industrial assets, IIoT is enabling the provision of new value-added services for “on demand” maintenance and support.[1]
The global market for IIoT sensors, networks, and compute power is growing rapidly. In 2021 it was sized at over US$263 billion and is expected to reach some US$1.11 trillion by 2028.[2] As the volume of connected devices continues to increase exponentially, enterprises are looking for solutions to help them manage and interpret the data being created.
The Growing Use of Industrial IoT
With the advent of cloud computing providing low-cost storage, edge computing devices, and the falling price of sensors of all kinds, IIoT has become a practical reality in the last 10 years. Many benefits have been claimed for the use of IIoT and some of these are summarized below:
- Remote Operations: IIoT makes it possible to visualize, track, and control facilities and assets without staff having to be onsite.
- Predictive Maintenance: Through the use of sensors, IIoT allows anomalies or problems with equipment to be detected in real-time, minimizing downtime, improving productivity, and avoiding costly repairs.
- Process Optimization: Monitoring the entire production line helps identify bottlenecks, enabling optimization of any line’s accuracy, speed, and production volume.
- Sustainability: Continuous monitoring allows energy consumption to be predicted and optimized, not just for equipment but the overall production operation.
Although the use of IIoT devices has grown rapidly, the number of legacy networks and devices is still significant and are expected to be around for a long time. This means that new IIoT projects need to combine new devices and technology with legacy systems and equipment. There are no easy answers at this stage as standards for interoperability between IIoT and networks that include “non-smart” legacy equipment are still emerging.
As the adoption of IIoT continues and devices become more capable, opportunities are emerging for manufacturers and operators of industrial assets to work together. This allows each party to focus on their strengths―optimizing machine operations and efficiently managing factory output respectively. This has led asset manufacturers to increasingly provide services to proactively monitor equipment in use by their customers and switch from scheduled to “on demand” support and maintenance, relieving the asset operator of the responsibility. As well as providing a means to increase customer satisfaction and develop a new revenue stream, this approach provides asset manufacturers with valuable feedback on product usage and issues leading to proactive solutions for current and future products.
Recently, many organizations have begun experimenting with “digital twins”―accurate models of machines and factories that combine data from many different sources (i.e., IIoT sensor data, software and hardware configurations, maintenance histories, etc.). In many cases these digital twins are using 3D design and simulation data to complement the operational information and provide a complete model that can be used to monitor usage and forecast future events. Digital twins present a holistic view of information about the asset and are creating new opportunities for operators to optimize use of their machines and for manufacturers to provide enhanced customer services.
All of these changes can be seen as part of the digital transformation of the factory. Digital transformation is a strategy for dramatically improving business operations, including profit margins, quality, and speed to market by leveraging data, corporate knowledge, and information technologies in a highly effective and efficient manner. A key facilitator of digital transformation in industrial companies will be the convergence of Operational Technology (OT) with Information Technology (IT) and Engineering Technology (ET). This convergence promises to accelerate the evolution of IIoT from a stand-alone technology to an integral part of the overall computing strategy of both machine operators and manufacturers.
Harnessing the Potential of IoT for Industry
CONTACT Software has many years of experience of supporting industrial asset operators and manufacturers. Their flagship product in this space is CONTACT Elements for IoT―a standards-based platform that provides comprehensive capabilities to display, monitor, and evaluate the history and current state of industrial assets. It is used as an IoT-enabled asset management system which can be expanded by standard modules for either service management or shop-floor management, depending on the customers’ needs.
CONTACT Software's solution, as illustrated in Figure 1, allows users to fully monitor and control their machines and factory environment in one place. The solution can be quickly configured to create a digital twin of the customer’s asset and factory environment, and define rules for identifying events and desired responses including alerts. Comprehensive data analytics simplify tasks like problem identification, machine monitoring, maintenance scheduling, energy optimization, and many others.
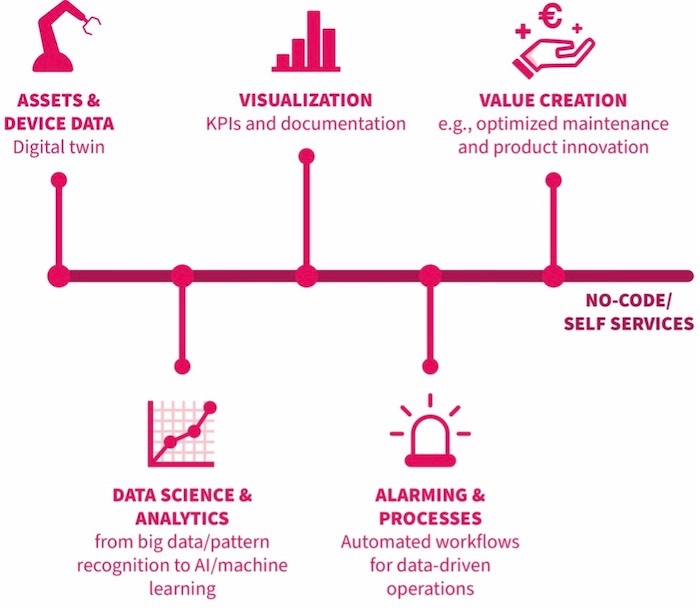
Figure 1―CONTACT Elements Architecture
(Courtesy CONTACT Software)
The modular software, as delivered by CONTACT Software, features low-code/no-code development tools, requires minimal customization, and can be implemented in as little as 30 days including customization. The solution typically runs at the enterprise level but can also operate on an edge computing device. In the case of enterprise level deployments, customers have the option to run the solution either on-premises, in their own cloud, or in the CONTACT Software cloud.
Additionally, CONTACT Software offers a Proof of Concept to demonstrate the value of their solution and access to experienced consultants who can help clients to build a business case.
Customer Case Studies
thyssenkrupp Dynamic Components
thyssenkrupp Dynamic Components is a leading global manufacturer of powertrain components. The company produces annually a total of 27 million camshafts, variable valve train systems, and rotor shafts for internal combustion, hybrid, and electric engines at 10 locations on several continents. Dynamic Components is part of thyssenkrupp’s Automotive Technology business. The powertrain specialist ensures end-to-end PLM processes with CIM Database and real-time production control with CONTACT Elements for IoT.
HBC-radiomatic
HBC-radiomatic is the global technology leader in industrial radio controls. Their innovative products are designed to ensure the safe and convenient operation of machines in a wide variety of industries. These include lifting and loading cranes, excavators, concrete pumps, and heavy-duty transporters. The company provides quality and service to its customers with its global partner network. With a service portal based on CONTACT Elements for IoT, HBC accelerates global service processes and combines the advantages of PLM and IoT to improve development methods.
CONTACT Software Background
CONTACT Software was founded in 1990 with the objectives of making complex product data more accessible and connecting employees across technical and organizational boundaries.
CONTACT Software has pioneered a number of innovative operating concepts including CIM Database; AgileRules, a methodology for development projects that allows objectives to be achieved more reliably; CONTACT Workspaces, for more efficient collaboration between teams and companies; and CONTACT Elements for IoT, a platform for solutions for data-driven processes using digital twins of industrial assets.
CONTACT’s customers operate in a number of markets and include the following examples:
- Automotive: thyssenkrupp Dynamic Components, KIRCHHOFF Automotive.
- Industrial Equipment: SIG Combibloc.
- Medical Devices: Olympus Surgical Technologies Europe.
- High-Tech Electronics: Weidmüller Interface.
- Consumer Products: ABUS August Bremicker Söhne.
- Logistics & Infrastructure: EWE Netz.
Conclusions
From its early beginnings with PLCs connected to proprietary networks, the usage of IIoT devices has expanded rapidly across industry and is expected to triple over the next five years.
Industrial users of capital assets are benefitting from the use of IIoT to improve asset uptime and improve maintenance management, while asset manufacturers are growing their businesses and cutting their costs through the provision of “on demand” services for maintenance and support.
As IIoT usage grows, the need for solutions to help users remain in control and extract the maximum benefits from their IIoT investments becomes more acute. One such solution is provided by CONTACT Software, who has long experience in supporting the use of IIoT for improving the management of industrial assets. Their modular, flexible platform (CONTACT Elements for IoT) is easily implemented and is already in use with many organizations across multiple industries. Industrial companies who are committed to the use of IIoT are encouraged to review and evaluate the CONTACT Software solution.
[1] Research for this commentary was partially supported by CONTACT Software.
[2] https://www.statista.com/statistics/611004/global-industrial-internet-of-things-market-size/